Numerical control machining is a multidisciplinary integrated high-tech integrating computer, automatic control, modern measurement, microelectronic control and information processing. It has been rapidly developed and greatly popularized in the field of modern industrial manufacturing. The use of CNC machining technology can meet the processing and manufacturing of multi-variety, high-volume, high-precision and complex parts. It is an important basic guarantee for the realization of industrial manufacturing automation, digitization, flexibility, informationization, integration and networking. It is also a modern machine tool. The soul and core of equipment has broad application and market prospects, and vigorously develops localized numerical control systems and functional components with independent intellectual property rights, which will promote the rapid development of China’s equipment manufacturing industry, promote the process of industrial modernization, and realize "Made in China" The move towards "Chinese Innovation" is of very important strategic significance.
1. The concept of CNC system
The numerical control system inputs corresponding data to the computer through the control of position, speed, trajectory and other parameters. The ideal motion trajectory is obtained after the system's automatic interpolation calculation, and then output to the actuator to process parts that meet the specified requirements. As the most important "brain" and "nerve center" of CNC machine tools, the CNC system plays a vital role in ensuring product quality and meeting user needs. It is an important symbol and concrete manifestation of the intelligent level of a country's machinery manufacturing industry. .
Numerical control systems generally use several microprocessors to realize numerical control processing functions in the form of programmed software, which are mainly composed of three basic units of input, processing and output, and all these tasks are centralized and rationally coordinated by the computer numerical control system through programs. Distribution, so that it can run and work efficiently, safely and reliably. The core of the CNC machine tool is the CNC system, which is equipped with a computer control system to meet the automatic processing of the machine tool. The CNC system can efficiently process the logic program specified by the control code or other instruction symbols, and input the code to the CNC device through calculation. After processing, the numerical control device sends out various control commands and signals to control the prescribed actions of the machine tool, and automatically process the parts according to the size and shape required by the product drawing. CNC machine tools have better solved the technical problems of processing complex, precise, small batch, and multi-variety parts. It is a flexible, efficient, and typical mechatronics product. CNC machine tools were born as a result of human civilization in the 19th century. An important sign, conforms to the needs of the development of the times, promotes the process of industrial revolution, and represents the forward direction of modern machine tool control technology. The integrated control principle of CNC system is shown in Figure 1.
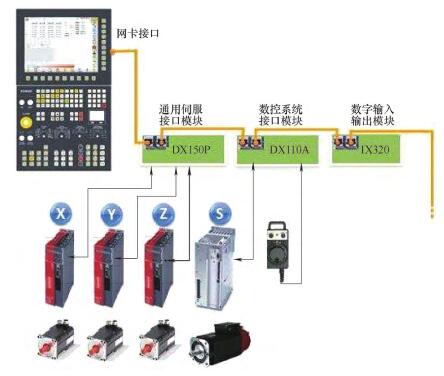
Figure 1 Integrated control principle of CNC system
2. Application status of domestically produced CNC system
CNC system is the core component of CNC machine tool equipment. The complete CNC machine tool needs to be equipped with CNC system when it leaves the factory. At the same time, the equipment transformation and system upgrade also need the CNC system. Especially in the past few years, my country's energy, electric power, aviation, aerospace, railway The rapid development in the direction of, automotive and metallurgy has provided a broad market space for the application of CNC systems.
Since the reform and opening up, China’s national economy has continued to grow steadily, and great social demand has driven the rapid development of the numerical control technology industry chain. At the same time, it should be noted that there is still a certain gap between China and foreign advanced numerical control technology, but this gap is in Gradually shrinking, on the basis of introducing, digesting, absorbing and re-innovating foreign advanced numerical control technology, China has produced numerical control systems and numerical control machine tools with independent intellectual property rights, especially domestic economical numerical control systems. The technical supporting requirements meet the actual use level of most Chinese users, and the price advantage has won the favor of the majority of users, forming a large-scale production advantage. Domestic CNC system companies have occupied more than 95% of the market share of economic CNC systems in my country. In the field of medium-sized numerical control systems, the functions of domestic numerical control systems have reached or approached the level of similar foreign products. The market price and after-sales service still have greater advantages than foreign products, and the market share is also rising. In terms of high-end CNC systems, domestic CNC systems have a small market share, and most of the market is occupied by foreign brands such as FANUC, Siemens, Mitsubishi, and DMG. However, it is gratifying that localized CNC systems have begun to enter this market. A high-end field, in which the research and development of Huazhong CNC and Guangzhou CNC are ready to go. With the major breakthroughs in key technologies through intensive research in the future, catching up with the international advanced level is just around the corner.
Although the research and development of CNC systems in my country has made great progress, more than 90% of the CNC systems supporting the high-end CNC field are foreign products. The high-end CNC system is an important means to meet the national strategic development of equipment, and it is a decisive factor in determining the performance, function, reliability and cost of machine tool equipment. In this core area, foreign countries still impose strict technical blockade on my country, which seriously restricts my country. The development of high-end CNC machine tools. In order to accelerate the rapid development of my country's CNC technology industry, the state has issued a series of policies, including the State Council’s approval of the implementation of the "Equipment Manufacturing Industry Adjustment and Revitalization Plan" and the national science and technology major project "High-end CNC Machine Tools and Basic Manufacturing Equipment". The "Equipment Manufacturing Industry Adjustment and Revitalization Plan" clearly stated: "Insist on the combination of equipment autonomy and key construction projects, adhere to the combination of independent development and introduction, digestion and absorption, and adhere to the basic principles of combining the development of the complete machine with the improvement of the basic supporting level", Increasing the market share of basic accessories such as CNC systems is an important part of implementing equipment autonomy. The national science and technology major project "High-end CNC machine tools and basic manufacturing equipment" also proposed that by 2020, the market share of domestic high-end CNC machine tools should be increased to a greater extent. These measures have created a good external atmosphere for my country's CNC technology industry, and are of great practical significance for the development of high-end CNC machine tools that meet the urgent needs of my country's defense industry.
At present, my country is in a period of rapid industrialization. The basic industries led by energy, electric power, aviation, aerospace and railways have a strong momentum of development, which constitutes a huge demand for machine tools, especially CNC machine tools. The development of complete functions, reliable performance and The technologically forward-looking CNC system is our historic choice. The application scenario of digital technology is shown in Figure 2.
Figure 2 Application scenarios of digital technology
3. The development trend of localized CNC system
The numerical control system is the prerequisite and important guarantee to ensure the leading technology of numerical control machine tools. The following points are predicted for the development trend of localized CNC system in the next few years:
(1) To develop towards high speed and high efficiency. The CNC machine tool realizes high-speed processing, which can greatly improve the processing efficiency, reduce the use cost, and can also provide a powerful technical guarantee for improving the surface processing quality and accuracy of the product.
(2) Develop towards high precision. By setting the automatic gap compensation function and automatic monitoring and automatic compensation of the servo system drift function, it can meet the requirements of manufacturing from precision machining to ultra-precision machining, and precision levels from micron to sub-micron and even nanometers, which will bring about the processing of high-precision products. Gospel.
(3) Develop towards high reliability. The numerical control system adopts large-scale application-specific integrated circuits and high-speed microprocessors, and through strict screening and verification in the manufacturing process, the reliability of the circuit is greatly improved. With the rapid development of digital technology, the reliability of CNC machine tools in the future has become an important indicator to measure the quality of CNC systems.
(4) Develop towards a composite and flexible direction. In order to reduce the auxiliary time of machine tools as much as possible and meet the needs of flexible production, people hope to integrate different processing functions on the same machine tool. Therefore, machine tools with compound functions have become one of the development trends of CNC systems in recent years.
(5) Develop towards multi-axis. In order to meet the processing requirements of various curved surfaces on the part surface, the use of multi-axis linkage machine tools can realize the rapid processing of parts under the condition of one clamping, significantly improve the accuracy level of the processed surface, and greatly increase the processing efficiency. Therefore, the development of axis CNC processing equipment has become An important means to adapt to market changes.
(6) Develop towards an open direction. The open CNC system allows users to easily integrate the user's special needs and technical know-how into the system by changing, adding or cutting CNC functions on a unified operating platform, and quickly realize a multi-variety, multi-level open CNC system , To form a brand-name effect with market competitiveness.
(7) Develop towards intelligence. Intelligent processing is a processing technology based on neural network control, fuzzy control, digital network technology and theory. Through the simulation of artificial intelligence activities in the processing process, it can solve many uncertain technical problems in the processing process that require manual intervention. Intelligent technology covers all levels of the CNC system. It includes adaptive control technology for processing, intelligent optimization of processing parameters, intelligent fault self-diagnosis and self-repair technology, intelligent fault playback and fault simulation technology, and intelligent AC servo drive device Wait.
(8) Develop towards networking. The realization of networked CNC machine tools enables the networked connection of its own CNC system with other external control systems or upstream computers, paving the way for the realization of functions such as man-machine dialogue and remote communication services. The networking of the numerical control system will greatly meet the information integration needs of production lines, manufacturing systems and manufacturing enterprises, and it is also an important means and necessary condition for realizing a new manufacturing model.